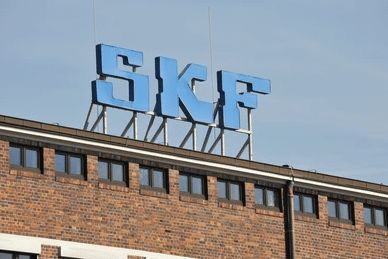
Introduction:
The impact resistance of bearings is a crucial factor in various industrial applications, especially those subject to shock loads, vibrations, and heavy impacts. NSK and SKF, two prominent bearing manufacturers, approach the challenge of impact resistance with distinct engineering and design philosophies. In this comprehensive comparison, we explore the impact resistance of NSK bearings versus SKF bearings, highlighting the factors that differentiate them and their significance in demanding applications.
Understanding Impact Resistance:
Impact resistance in bearings refers to their ability to withstand and absorb sudden shock loads, ensuring that the bearing maintains its structural integrity and performance. This is vital in applications where impacts and vibrations are common operational conditions.
NSK Bearings:
NSK is renowned for its precision engineering and a commitment to optimizing impact resistance in their bearing designs. Several key factors contribute to their bearings’ exceptional performance in this aspect:
High-Strength Materials: NSK employs high-strength materials that enhance the bearing’s ability to withstand shock loads and prevent deformation or breakage.
Advanced Cage Designs: NSK’s cage designs are engineered to provide optimal load distribution within the bearing, reducing the risk of localized stress and enhancing impact resistance.
Shock-Absorbing Lubrication Solutions: NSK offers shock-absorbing lubrication options that help reduce the transmission of impact forces through the bearing, safeguarding its internal components.
Customization for Impact Resistance: NSK provides customization options for applications with unique impact resistance requirements, ensuring the bearing can withstand and absorb shocks effectively.
Rigorous Testing: NSK’s quality control processes include comprehensive testing for impact resistance, confirming that their bearings can perform reliably under shock loads and vibrations.
SKF Bearings:
SKF, another esteemed manufacturer, prioritizes impact resistance in its bearing designs. The following features set SKF bearings apart in terms of performance under shock loads:
High-Strength Materials: SKF employs high-strength materials that maintain the bearing’s structural integrity and performance even when subjected to heavy impacts.
Cage Designs for Load Distribution: SKF’s cage designs are engineered to provide optimal load distribution within the bearing, reducing localized stress and enhancing impact resistance.
Shock-Absorbing Lubrication Solutions: SKF offers shock-absorbing lubrication options that help dampen impact forces, protecting the bearing’s internal components.
Customization for Impact Resistance: SKF provides customization options for applications with unique impact resistance requirements, ensuring the bearing can withstand and absorb shocks effectively.
Comprehensive Quality Control: SKF’s stringent quality control processes include thorough testing for impact resistance, confirming that their bearings can perform reliably under shock loads and vibrations.
Conclusion:
Impact resistance is a critical parameter in industries where shock loads and vibrations are common operational conditions, and it is essential for the longevity and reliability of machinery in these environments. Both NSK and SKF are esteemed manufacturers, and each offers unique advantages in terms of impact resistance in their bearings.
NSK’s bearings are recognized for their precision engineering, high-strength materials, advanced cage designs, shock-absorbing lubrication solutions, customization options, and rigorous testing. These features make NSK bearings an excellent choice for applications where impact resistance is of primary concern.
Similarly, SKF’s focus on precision engineering, high-strength materials, cage designs for load distribution, shock-absorbing lubrication, customization options, and comprehensive quality control ensures that their bearings excel in maintaining reliable performance under heavy impacts and vibrations.
The choice between NSK and SKF bearings for applications that demand high impact resistance depends on the specific requirements of the application. Careful consideration of factors such as the magnitude and frequency of impact loads, operating conditions, and customization options will enable you to make an informed decision to optimize the performance and longevity of your machinery under these demanding conditions.