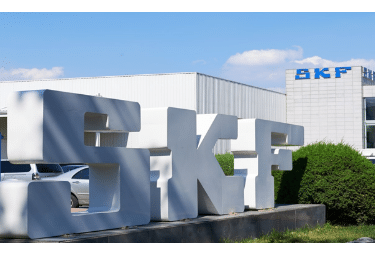
Introduction:
Innovation in design and engineering technology plays a crucial role in advancing the performance and capabilities of bearings. SKF and TIMKEN, two renowned manufacturers in the bearing industry, continuously invest in innovative design concepts and engineering technologies to meet evolving customer demands and industry requirements. This article provides an in-depth exploration of the innovative design approaches and engineering technologies employed by SKF and TIMKEN in their respective bearing solutions.
SKF Bearings:
Innovative Design:
Modular Solutions: SKF adopts a modular design approach, enabling the customization and configuration of bearings to suit specific application requirements. Modular components facilitate easy interchangeability, simplifying maintenance and reducing downtime for end-users.
Integrated Sensor Technology: SKF integrates sensor technologies into its bearing designs, allowing real-time monitoring of various parameters such as temperature, vibration, and lubrication condition. These smart bearings provide valuable insights into equipment health and performance, enabling proactive maintenance and predictive analytics.
Advanced Sealing Solutions: SKF develops innovative sealing solutions to enhance bearing protection against contaminants, moisture, and harsh operating environments. From labyrinth seals to lip seals and magnetic encoders, SKF’s sealing technologies prolong bearing life and improve reliability in challenging conditions.
Engineering Technology:
Computational Modeling: SKF employs advanced computational modeling techniques, such as finite element analysis (FEA) and computational fluid dynamics (CFD), to simulate bearing behavior and optimize performance. Virtual prototyping enables SKF engineers to evaluate design iterations rapidly and identify potential improvements before physical testing.
Tribology Expertise: SKF’s extensive expertise in tribology—the science of friction, lubrication, and wear—drives innovations in bearing materials, surface coatings, and lubrication systems. By understanding and controlling frictional interactions, SKF optimizes bearing performance, efficiency, and longevity.
Sustainable Manufacturing: SKF integrates sustainable practices into its engineering processes, focusing on resource efficiency, waste reduction, and eco-friendly materials. The company’s commitment to sustainable manufacturing aligns with global environmental initiatives and reinforces its reputation as a responsible corporate citizen.
TIMKEN Bearings:
Innovative Design:
Precision Engineering: TIMKEN’s precision engineering capabilities enable the design and manufacture of bearings with tight tolerances and high accuracy. The company leverages advanced machining techniques, such as CNC grinding and honing, to achieve precise geometries and surface finishes critical for optimal performance.
Customized Solutions: TIMKEN offers customized bearing solutions tailored to specific customer requirements, including special dimensions, configurations, and materials. Collaborative design processes ensure that TIMKEN bearings meet the unique challenges of diverse industries and applications.
Advanced Lubrication Systems: TIMKEN develops innovative lubrication systems, including automated greasing systems and solid lubricants, to enhance bearing performance and reliability. These lubrication solutions minimize friction, reduce wear, and extend bearing service life in demanding operating conditions.
Engineering Technology:
Materials Science: TIMKEN invests in materials research and development to identify and utilize advanced alloys, polymers, and composites for bearing components. By selecting optimal materials based on performance requirements and application conditions, TIMKEN enhances bearing strength, durability, and resistance to wear and corrosion.
Finite Element Analysis (FEA): TIMKEN employs FEA simulations to analyze bearing performance under various loads, speeds, and environmental factors. By modeling stress distribution, deformation, and thermal effects, TIMKEN engineers optimize bearing designs for maximum reliability and longevity.
Continuous Improvement: TIMKEN fosters a culture of continuous improvement in engineering practices, leveraging feedback from field performance data, customer input, and internal research to drive innovation. The company’s commitment to ongoing refinement ensures that TIMKEN bearings remain at the forefront of technology and performance excellence.
Conclusion:
Innovation in design and engineering technology is instrumental in shaping the performance, reliability, and versatility of SKF and TIMKEN bearings. Both companies demonstrate a commitment to pushing the boundaries of bearing technology through modular design concepts, sensor integration, computational modeling, precision engineering, advanced materials science, and sustainable manufacturing practices. By embracing innovation, SKF and TIMKEN empower customers with cutting-edge bearing solutions that optimize equipment performance, minimize maintenance costs, and drive operational efficiency in diverse industrial applications.