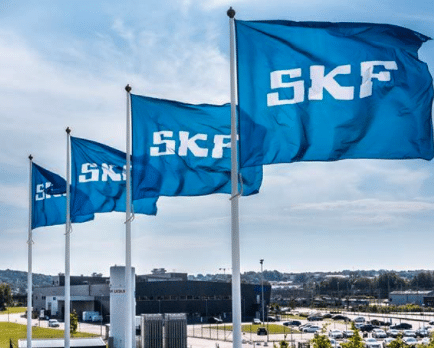
Introduction:
The metallurgical industry relies on precision, durability, and performance to ensure the efficient processing of metals. Bearings are critical components in metallurgical applications, from rolling mills to smelting equipment. NSK and SKF, two renowned bearing manufacturers, have a significant presence in the metallurgical sector. In this comprehensive comparison, we will explore NSK bearings and SKF bearings for metallurgical applications, highlighting their unique features, performance, and significance in the industry.
Challenges in Metallurgical Applications:
The metallurgical industry presents unique challenges, including:
High Temperatures: Metallurgical processes involve extreme temperatures, requiring bearings that can withstand heat and thermal expansion.
Heavy Loads: Equipment in this sector often handles heavy loads, demanding robust bearing design and high load capacity.
Precision and Accuracy: Metallurgical processes demand precision and accuracy in the rolling, shaping, and cutting of metals.
Reliability and Durability: Bearings must perform reliably in harsh environments and have a long service life to minimize downtime and maintenance costs.
NSK Bearings for Metallurgical Applications:
NSK has a reputation for delivering high-performance bearings suitable for metallurgical applications. Key features and advantages include:
Advanced Material Technology: NSK employs advanced materials and coatings to enhance bearing durability and resistance to heat, corrosion, and wear, crucial for metallurgical environments.
Precision Engineering: NSK’s precision engineering processes result in bearings with minimal dimensional variations and tight tolerances, essential for maintaining reliable and accurate metallurgical processes.
High-Temperature Performance: NSK offers bearings designed to withstand extreme temperatures, ensuring stability and safety in metallurgical operations.
High Load Capacity: NSK designs bearings to handle heavy loads, a critical requirement in the metallurgical industry.
Reliability and Durability: NSK bearings are engineered for reliability and durability, reducing downtime and maintenance costs.
Customization: NSK provides customization options to tailor bearings for specific metallurgical applications, ensuring optimal performance and longevity.
SKF Bearings for Metallurgical Applications:
SKF is also a prominent player in the metallurgical industry, offering bearings designed for optimal performance in metallurgical applications. Key features and advantages include:
Advanced Materials: SKF utilizes high-quality materials and coatings to enhance bearing durability, wear resistance, and resistance to heat and corrosion, vital for metallurgical applications.
Precision Engineering: SKF’s precision engineering processes result in bearings with minimal dimensional variations and tight tolerances, ensuring precise and accurate metallurgical processes.
High-Temperature Performance: SKF offers bearings capable of withstanding extreme temperatures, ensuring safety and stability in metallurgical operations.
High Load Capacity: SKF bearings are engineered to handle heavy loads, contributing to the efficiency and safety of metallurgical processes.
Reliability and Durability: SKF bearings are designed for reliability and durability, reducing maintenance costs and downtime.
Customization: SKF provides customization options to ensure that bearings meet the specific requirements of different metallurgical applications, delivering optimal performance and longevity.
Conclusion:
In the metallurgical industry, where extreme temperatures, heavy loads, precision, and reliability are of paramount importance, both NSK and SKF have established themselves as trusted providers of high-performance bearings.
The choice between NSK and SKF bearings for metallurgical applications should consider specific requirements such as high-temperature performance, load capacity, precision, reliability, and customization needs. By carefully assessing these factors, metallurgical professionals can make informed decisions that enhance the efficiency and safety of metallurgical processes, ensuring the quality and integrity of metal products.